What is ERP for Alcohol Industry?
ERP for alcohol manufacturing industry manages all business activities, including acquiring raw materials, manufacturing finished products, getting a real-time status of the stock & inventory, payment management, supplier management, and displays these details on a single platform. The best part is that you don’t need to depend on multiple systems for managing your data. ERP Software is a one-stop shop that takes care of all your alcohol & distillery needs.
The business management software will allow you to spend more time brainstorming strategies and studying market realities instead of handling the administrative side of the business.
What are the Major Challenges in Alcohol Industry?
Complex Government Regulations
Alcohol and distillery manufacturing companies are continuously monitored by regulations as well as reforms. Also, one major issue for this industry is that the latest tax regime under GST does not encourage the consumption of alcohol and beverages.
Constantly overlapping tax structure also becomes a critical challenge for the industry. When it comes to specific drinks like beer, every state has different rules which makes its manufacturing process tough.
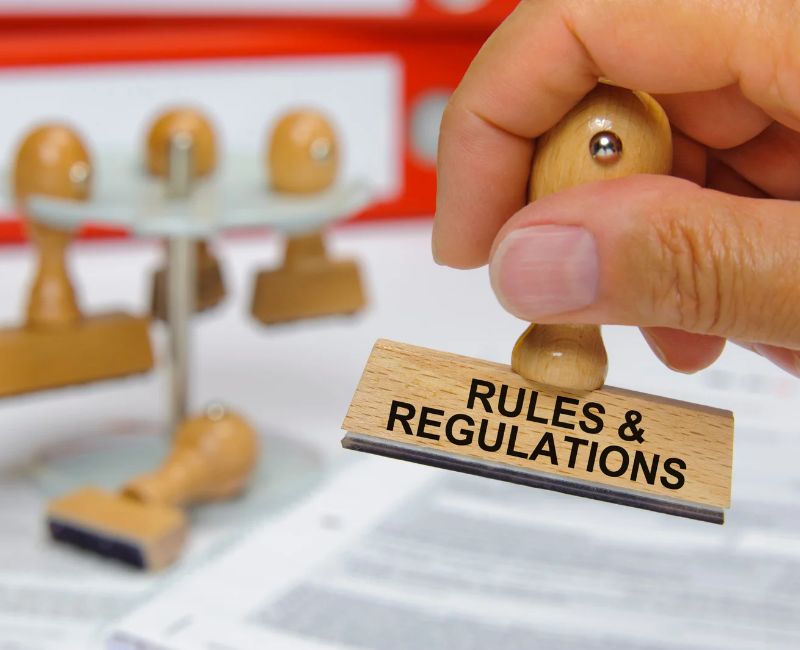
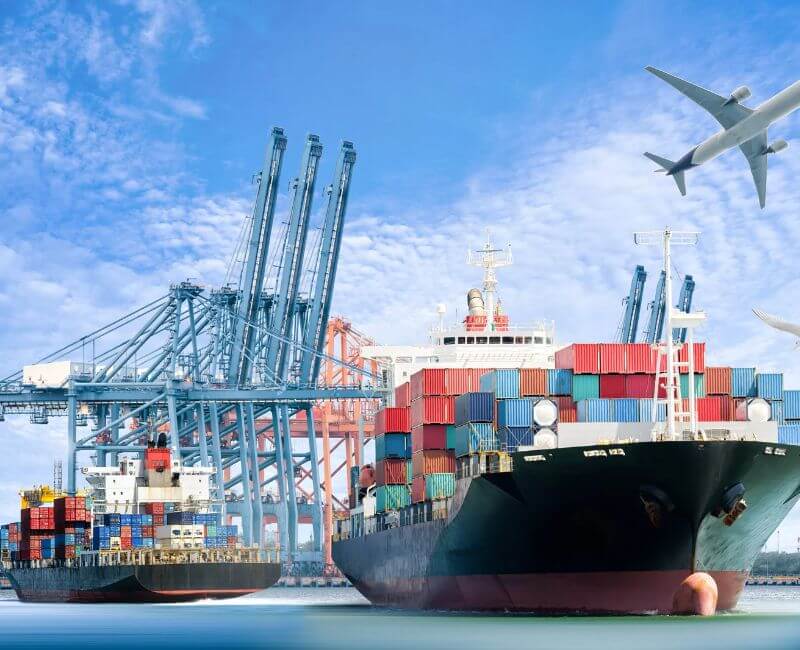
Disrupted Logistics
The logistics market is often disorganized and also the infrastructure is down due to bad road and network conditions. Also, insufficient distribution channels, as well as bad quality products, are some major concerns that affect the manufacturing of beverage companies. These factors result in logistics expenses leading to increased pre-production expenses compared to other countries.
High Demand for Healthy Drinks
Today, consumers are looking for healthy drinks that do not include any synthetic elements. Scientists have observed that there has been a sharp fall in the demand for processed drinks at the present time.
People are becoming more aware of the consumption of natural drinks and have become thoughtful about their impact on their health. Alcohol & beverage manufacturing companies should discover various methods to fight this rising challenge.
Limitations of Innovation
Since the competition is quite intense in the alcohol and distillery industry, manufacturers are required to invent innovative products. But, the market has a variety of products with the same term and characteristics. This has remained the issue for years which clearly indicates that innovation is limited in this sector.
Features of Alcohol Manufacturing ERP
Attach different product IDs and descriptions, such as UPC, and SKU, to each product. Find out the actual cost using the multi-currency feature. with inventory management software. Also, Control and manage the processing and fulfillment through the barcoding software. Also, control and track raw materials and finished goods.
Design marketing strategies based on product profitability to improve ROI. Create a better supply chain strategy by gathering product-level sales information. You can also save costs based on geography, demography, psychography, and behavioral trends with this sales management system.
Sage X3 ERP enterprise resource planning will allow you to re-order items as soon as the quantity of raw material goes below the predetermined threshold. Assess the purchase quality of each product and keep a minimum stock quantity based on expected demand with the ERP alcohol.
Explore detailed customer records. Analyze KPIs and KRAs in real-time and keep operational expenses for the business under control using historical data. Also, brainstorm effective strategies by analyzing customer trends with the outstanding alcohol manufacturing ERP solution.
The ERP alcohol finds out how much payment is due per customer/vendor/supplier. Modify limits for credit-worthy customers. Get automatic reviews of credit status when a new sales order or sales quote is added to the system.
Set predefined credit limits to ensure that auto-buying of raw materials is restricted above a particular limit with Sage 300 ERP.
Future-Proof Your Business with Sage X3
Empower your team and elevate your results with ERP Software
Benefits of ERP for Alcohol Manufacturing Industry
Inventory Management
ERP software for spirit manufacturing enables tracking inventory — raw ingredients and finished products. It also helps with the packaging and distribution of manufactured items. The Material Requirements Planning (MRP) feature of Sage X3 will assist you with everything from planning and purchasing to scheduling based on past records and future predictions.
The MRP module of the distillery ERP also helps to reduce costs and minimize waste by keeping required inventory levels in the warehouse. Moreover, this distillery software is specially equipped to maintain daily, monthly, and yearly records of transactions, operations, and physical inventory without any errors.
Quality Control & Testing
Sage X3 ERP for spirit manufacturing ensures top-notch quality for all alcoholic products you manufacture. To ensure consistent color, aroma, and taste, it considers various factors, including pH levels, gravity, yeast genealogy, and fermentation levels.
In addition, the quality control ERP helps store customer-specific and in-process test results for fermentation and packaging to ensure consistent quality. It also verifies and manages quarantined materials from vendors and suppliers.
Regulations and Compliances
Sage X3 is one of the best distillery solutions in the industry as it helps you adhere to stringent government regulations apart from helping you manage your business.
It efficiently handles labels, licenses, permits, and taxes and ensures you adhere to the rules and regulations created by a specific state, country, or international institution.
Today, governments globally want companies to abide by complicated regulatory requirements. Sage X3 alcohol manufacturing ERP is an industry-specific software that provides top-notch recordkeeping facilities and reporting functionality.
Integrated Accounting
Sage X3 distillery ERP manages accounting activities like a pro. It automatically creates journal entries about the products and by-products produced during the process of manufacturing activities. It captures the real-time costs of raw materials and finished products and the cost of goods sold.
This software also allows the monitoring of all accounting & financial activities through integrated analytics and reporting tools. You can also control costs using the forecast feature that helps estimate product costs based on market conditions and changing customer preferences.
Schedule Product Tour
"*" indicates required fields